Obdii vs Can: On-board diagnostics, OBD2, is a ‘higher layer protocol’ (like a language). CAN is a method of communication.
On-board diagnostics, commonly known as OBD2, serves as a crucial component in modern vehicles by providing valuable insights into their performance and detecting potential issues.
It acts as a higher layer protocol akin to a language that allows various vehicle systems to communicate with each other seamlessly.
In contrast, Controller Area Network (CAN) serves as the underlying method of communication used within the on-board diagnostics system.
Together, these two elements play an integral role in ensuring efficient automotive operations and effective troubleshooting when problems arise.
The OBD2 standard acts like a universal translator for car systems; it defines how information should be exchanged between different components within the vehicle.
Think of it like speaking different languages but using one common dialect to understand each other better. CAN, on the other hand, provides the physical means for this communication to occur smoothly.
It enables data transmission at high speeds over twisted-pair wiring or through wireless connections.
Table of contents
Understanding On-board Diagnostics (OBD):
On-board diagnostics, also known as OBD, is a crucial system in modern vehicles that allows for the monitoring and reporting of various vehicle parameters.
It plays a vital role in diagnosing issues and ensuring optimal performance. Here’s what you need to know about OBD:
What is OBD?
On-board diagnostics (OBD) refers to the computerized system installed in vehicles to monitor their performance and emissions.
It provides real-time data on engine functions, such as speed, fuel consumption, temperature, ignition timing, and more.
The Purpose of OBD:
The primary purpose of OBD is to identify malfunctions or abnormalities within a vehicle’s systems.
By constantly monitoring the components and systems involved in vehicle operation, it can detect potential problems early on.
OBD Generations Generation Years Features OBD-I 1980s-1995 Basic fault code retrieval OBD-II 1996-present Enhanced diagnostic capabilities.
OBD-II Protocols:
The most common protocols used by OBD-II are:
Advantages of OBD:
OBD and CAN:
CAN (Controller Area Network) is a specific method of communication used by some OBD-II systems.
It allows for faster and more reliable data transmission between various vehicle components.
While all vehicles with OBD-II have the same basic functions, not all use the CAN protocol.
The Evolution of OBD2:
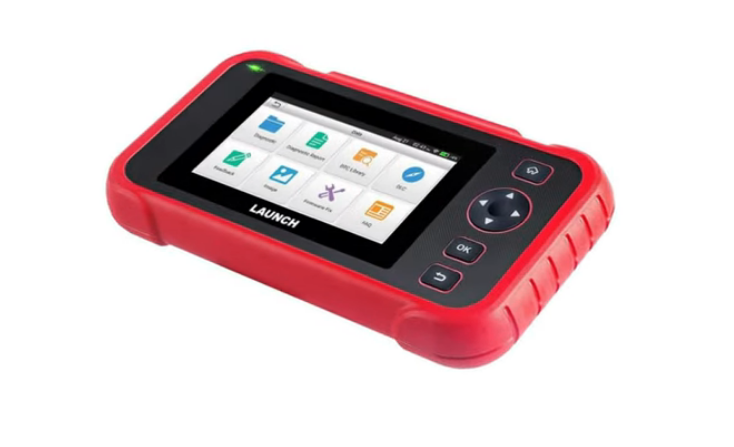
On-board diagnostics (OBD) systems have come a long way since their inception. This section explores the evolution of OBD2, focusing on its advancements and improvements over time.
Early OBD Systems
In the early days, vehicles were equipped with basic diagnostic systems that allowed mechanics to retrieve limited information about the engine’s performance.
These early systems relied on proprietary protocols and lacked standardized communication methods.
Introduction of OBD1
With the introduction of OBD1 in the late 1980s, automobile manufacturers started implementing standardized diagnostic capabilities in their vehicles.
OBD1 brought about a significant improvement by providing technicians access to more comprehensive data for troubleshooting purposes.
Need for Standardization
As technology advanced, it became clear that a unified approach was necessary to address compatibility issues between different vehicle makes and models.
This need led to the development of On-Board Diagnostics II (OBD2), which aimed at standardizing diagnostic protocols across all vehicles sold in the United States from 1996 onwards.
Advantages of OBD2
Advantages Improved Diagnostic Capabilities Enhanced Communication Protocols Compatibility Across Vehicle Brands OBD2 brought numerous advantages over its predecessor:
Improved Diagnostic Capabilities:
By expanding the range of monitored components and introducing standardized trouble codes, technicians gained access to more precise information regarding faults within an engine system.
Enhanced Communication Protocols:
Unlike earlier systems that used manufacturer-specific protocols, OBD2 relies on a standardized protocol called Controller Area Network (CAN).
CAN allows for faster and more efficient communication between various electronic control units (ECUs) within a vehicle’s network.
Compatibility Across Vehicle Brands:
OBD2 mandated the use of a standard diagnostic connector and allowed for universal access to vehicle data.
This facilitated easier diagnostics and repairs, as mechanics no longer needed multiple proprietary tools for different car brands.
Ongoing Development:
OBD2 continues to evolve, with newer versions introducing additional functionalities and improved diagnostic capabilities.
The latest iteration is OBD2+ which integrates wireless communication capabilities, enabling real-time monitoring and remote diagnostics.
Exploring the CAN Communication Protocol:
The CAN (Controller Area Network) communication protocol is a widely used method for exchanging information between electronic control units (ECUs) in vehicles.
It provides a reliable and efficient way to transmit data within an automotive network. Here, we will delve into the key aspects of this protocol:
Differences Between OBDII vs CAN:
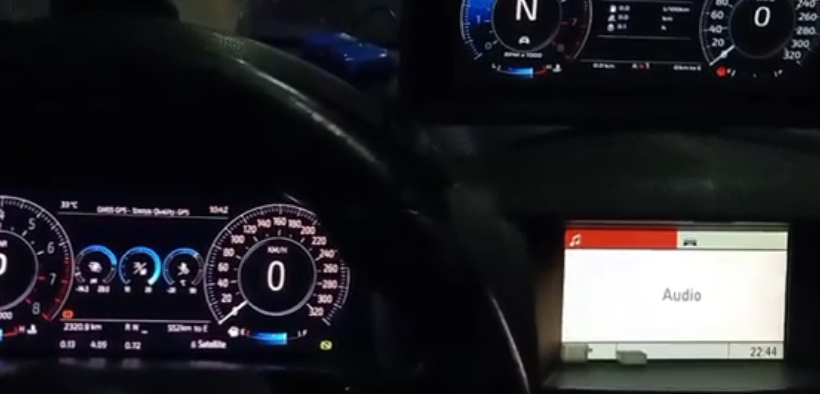
When it comes to on-board diagnostics (OBD), there are two important terms you need to be familiar with: OBDII and CAN.
While they are related, they serve different purposes in the world of automotive diagnostics. Let’s take a closer look at their differences:
OBDII:
On-board Diagnostics II is a standardized system that allows technicians and individuals to access information about the vehicle’s performance.
CAN:
Controller Area Network is a communication protocol that enables various electronic control units (ECUs) within a vehicle to communicate with each other.
Functionality:
OBDII: It acts as a higher layer protocol or language, providing a common set of rules for how diagnostic data should be communicated between the vehicle’s computer systems and external devices such as scanners or diagnostic tools.
CAN: It primarily serves as the method of communication between ECUs, allowing them to exchange information quickly and efficiently.
Compatibility:
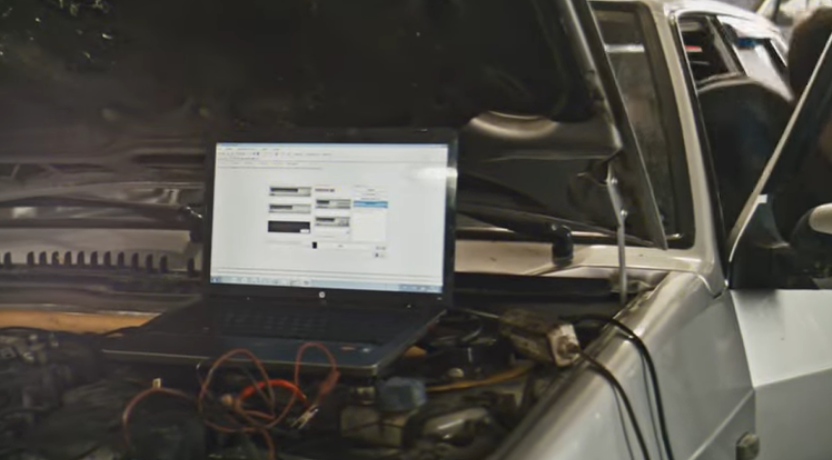
OBDII: This standard was introduced in 1996, making it mandatory for all gasoline-powered vehicles sold in the United States since then. It has become widely adopted globally.
CAN: Initially developed by Bosch in the mid-1980s, this communication protocol became prevalent around 2004 when it began replacing older protocols like J1850 PWM/VPW and ISO9141.
Data Transmission:
OBDII: It utilizes various protocols such as SAE J1850 PWM/VPW, ISO9141-2, ISO14230 KWP2000, and most commonly today—ISO15765-4 (CAN). These protocols define how data is transmitted over different physical layers.
CAN: As mentioned earlier, it uses its own distinct protocol known as Controller Area Network (CAN). It allows for high-speed, reliable data transmission and is widely used in modern vehicles.
Scope of Information:
OBDII: It provides access to a wide range of diagnostic information related to the engine, transmission, emissions systems, and other vehicle components.
CAN: While it enables communication between ECUs, it does not directly provide diagnostic information. However, it facilitates the exchange of data that can be interpreted by OBDII compliant devices or software.
Watch this video for faster response:
Benefits and Limitations of OBD vs. CAN:
OBD (On-board diagnostics) and CAN (Controller Area Network) are both essential components in modern vehicle systems.
While OBD2 is a higher layer protocol, similar to a language that enables communication between different vehicle modules, CAN serves as the method of communication itself.
Let’s explore the benefits and limitations of OBD compared to CAN:
Benefits of OBD:
Limitations of OBD:
While both technologies play vital roles in automotive diagnostics and communication systems today, OBD offers standardized diagnostic codes along with easy access to crucial information for enhanced maintenance planning.
However, CAN serves as the primary method of communication, enabling real-time data transmission between different vehicle modules.
Understanding the benefits and limitations of both OBD and CAN helps to optimize vehicle performance, maintenance, and troubleshooting activities.
Conclusion and final thoughts đź’
Overall, both OBD2 and CAN play vital roles in modern on-board diagnostics.
While OBD2 acts as the universal language enabling seamless interaction between different components within a vehicle’s network, CAN ensures smooth transmission of data across these interconnected systems.
With their combined functionality, these technologies contribute to improved maintenance practices and enhanced overall performance in today’s automotive industry.
Leave a Reply